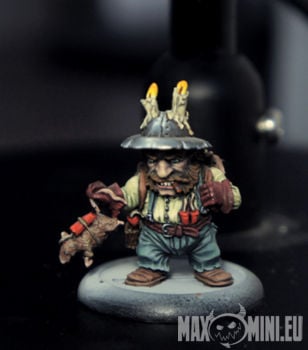
2014 Summary
Yup, it is this time of year ๐ . So if you’re not faint of heart and can stand mumblings of tabletop figures company guy read on.
In the last couple of weeks I’ve been trying to wrap up our workshop’s 2014 – what has changed, what went good and what went bad. Not an easy thing for me considering amount of things I’ve been involved in. So why do it you may ask? Well, I think it gives us a certain perspective and ability to catch a breath a tad. Which is definitely welcome considering the pace of the changes.
I’ll start with something you haven’t seen but I think it had greatest impact on us. The crew has changed – MUCH. Now I can safely say we have grown a TEAM – and yes , it is so important for me I had to write it in capital letters. It’s great to work with people that are passionate about what they do and the ones that actually understand it requires effort from their side. They motivate me and force me to organize myself – something I’ve not been very good at (one of the reasons cash is being handled by Kacper ๐ ) and something I still need to seriously work on.
Most the good things sparked from this simple thing and we really need to focus not to loose that, not allow bad habits to take roots.The efforts to learn new things (goldsmith course, new software, actively pursuing new prototyping and manufacturing methods) allowed us to work beyond our comfort zone. We’ve designed jewelry, worked on models for numerous other companies and participated in number of pretty exciting projects. Can’t share most of them because of NDA, but certainly one of the stars for us was designing a trophy for famous military unit “GROM”. It resulted in super cool 160mm model – check their fanpage . Crown jewel of the project was meeting “GROM” members in person and learning how awesome they are – my hats and respect goes to them!
This was a project we did with people from Academy of Arts in Warsaw – the initial idea spawned in Dominik Glab’s head and we have been tasked with sculpt execution ๐ . A reminder for us that if you are passionate about your work you will eventually meet people who are likewise-minded.
All those new ventures are super exciting for us. But at the same time I think we should be careful not to loose sight of our main joy – and that is tabletop models and fantasy. It is quite easy to loose focus with so many cool things around. I humbly admit that we may have made a step in that route. It will take some serious effort to figure out whether / how we can expand our line and work on external projects at the same time. Otherwise we will end up as simply a service house. Don’t get me wrong – nothing bad in that, but personally I simply enjoy developing our own IP . It would be a shame to loose that, especially considering how much we have already done.Heck, if you add things that are still not released…. Which brings me to a thing we should really commit to in 2015 – finalizing the things and releasing stuff that is ready. Our own first game is still in the works and we need to speed it up. So many models are already done and it’s a shame that so far they only decorate my desk. And, ok I know I’m kinda biased but damn, they’re so cool! But don’t take my word on it, check the attached pic of one of the dwarves.
With the tools we have sky is the limit. Basically we can handle models from start to finish (design, sculpt, prototype, manufacturing) without the need to outsource any of the tasks.
We’ve continued to expand our knowledge of using 3d tools. 3D Coat and Modo accompanied Zbrush and Rhino in our pipeline. Nowadays we can solve issues that would hamper many – we’ve grown to be very good when it comes to 3d designing manufacturable items . There’s still lot we could learn in this aspect though. I especially feel we’re under-utilizing Modo. With its rigging and simulation capabilities I’m sure we could add some amazing tricks – we still do, but I think we are only scratching the surface. The idea of coming up with lots of model variants, poses just to get the best ones really bugs me ๐ .
The thing that is still holding us back a tad are manufacturing capabilities. Doing more items in white metal helped for sure. The work of Chris, Robert and me resulted in us getting really confident with spincasting white metal.
But white metal is not an answer to all of the models. Making a large vehicle in white metal would be an effort in insanity ๐ .
The resin casting, something we’re really proud of, is painfully slow at the level we have reached. It became especially evident during handling some of the casting requests. I humbly admit – we were unable to keep some of the deadlines.
Scaling down number of requests we do and organizing them differently is one of the answers. But it is not a one that satisfies me entirely – especially the first part.
So we should address that. Easier said than done – question is how :D. One of the solutions might be actually getting some experimental tooling done and trying the new method we’ve conceptualized and tested in 2014. Other would be trying to release a plastic set.
I’m leaning towards first one for two reasons. First of all I’m still not sure the numbers would justify the cost of tooling for plastic (unless we find a workshop willing to work with bronze/brass cavities we could do by ourselves) . Then if the experimental method works we wouldn’t be limited in terms of shape as you can be with plastic.
But we shouldn’t forget about planning – it will not only save frustration on our customers side, but on ours as well. Desperately fighting with the deadlines has the impact on the team too – casters, mouldmakers, sculptors, basically the whole staff.
You may wonder – when the hell he’ll mention their first Kickstarter?! It was a big event for us, brought with the help of our amazing friends in London. The reception passed our expectations (BIG FAT THANK YOU!), it was a blast. It allowed us to work on a whole orc army – something that would be economically difficult otherwise and it was good lesson for the future. Crowdfunding really changes the game for companies as ours.
It was not all candy-dandy though – even though we prepared lots of models before the campaign it has turned out I was overly optimistic when it comes to finishing the the project. An even clearer to-do list for the future is needed and we have to be more careful when relying on external vendors. You see, as there were some rather big models involved I’ve decided to 3d print them outside the workshop. While our printer does an amazing job when it comes to small models it is too slow to work on larger ones. So I found juggling files between a couple of companies we’ve worked with in the past which seemed to take like forever.
The rather unexpected resolution was the purchase of the second machine to get the remaining vehicles done.
Among the things we did right with the campaign for sure the way we handled the order forms was spot on. We weren’t able to come with specialized web app – and that’s when you start to value tools that are already available. Using Google Docs spreadsheets with carefully set permissions was great and got rid of many annoying issues. For example – no email juggling, ease of transferring the data into our records so we can start sending the orders out . On top of that backers can fill the order from most of the devices (phone, pc etc).
But getting back to regular things – it seems we partially fixed packaging issues. New blisters are an improvement. Still no fancy boxes though. While I care first about models themselves, how good they are and how well cast they are, I realize that good product should be delivered in matching packaging. It seems a trivial thing, but if you don’t care about that you might end with an item that gets overlooked in the store or feels slightly “cheapish”. So we need to get those damn boxes worked out!
The problem with those comes from a fact that none of us is a 2d designer – atm we can’t make them ourselves. Graphic studios we’ve spoke with tend to be very expensive and most of the times they do not understand what we do – thus they come with mostly uninspiring designs for us.I doubt we will be able to afford a full-time inhouse 2d artist, but I have some hopes with the contacts we got during the projects I mentioned earlier. People like Glen Giron and Zuzanna Lapies already did some stellar job for the Green Alliance.
Once packaging gets done we should also further “prettify” our website. It’s so close to what I wanted it to be – I’d love for it to get this final polish.
There’s one major issue still not addressed – the community. We’re so busy with the daily duties (sculpting, answering emails, casting, sending orders and so on) that the articles, posting on FB, forums , spreading the news is left behind. And that’s a shame – one of the things I’ve always enjoyed was interacting with other hobbyists , exchanging feedback, providing help when able. The “social” part is IMO integral part of our hobby. I think I’m not really good at this though, I’m rather a forums “lurker” atm so leaving all the updates / posts to me simply can’t work. We need to activate the rest of the team in this aspect and see how they feel with it. Also I’d love to hear your thoughts and ideas what we can do in this matter.
2014 was tough, but amazing year. Started with me and Kacper being in rather poor moods and tired. Ended with a blast and with the team having renewed energy. Showed us first fruits of all the hard work we did. Looking forward for the things (especially good ones ๐ ) 2015 has in store for us.